Among the stope operation equipment, the electric scraper is at the heart and is the ruler of the mining capacity of the mine. Its automation level has strong reproducibility and promotion; at the same time, due to its poor working environment and heavy production tasks, it is urgent to liberate the scraper drivers, practice the essential safety concept of "The less people working underground the safer" in underground mining, and put forward the research on transformation for the remote scraper driving.
The target is to implement transformation for remote scraper driving, so as to solve the contradiction between the increasing production tasks and the bad on-site environment.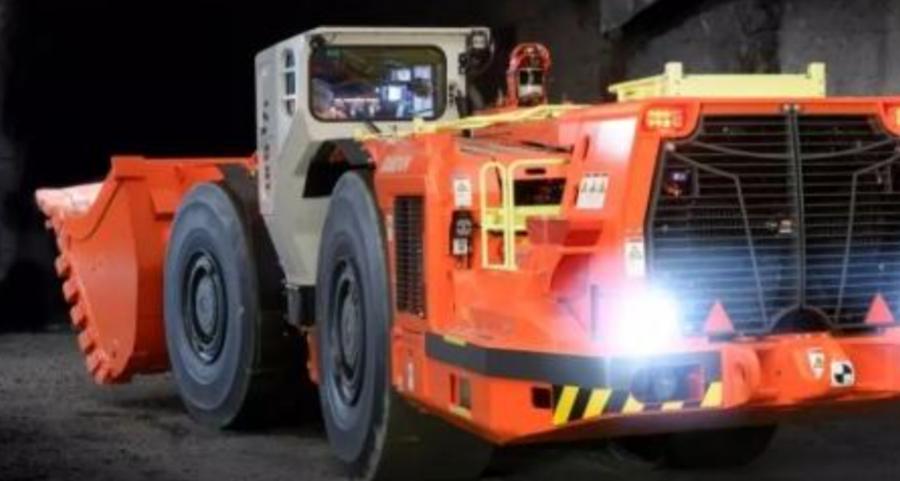
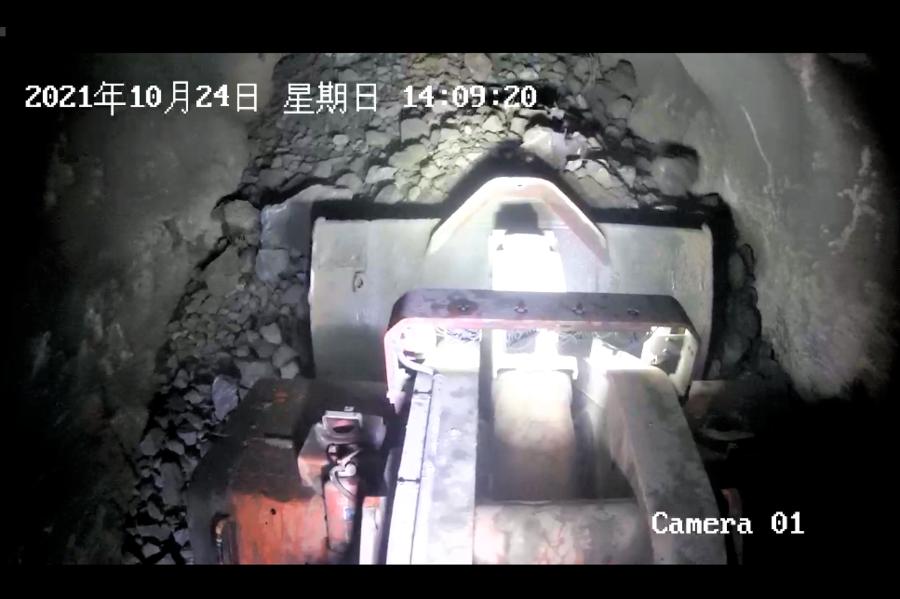
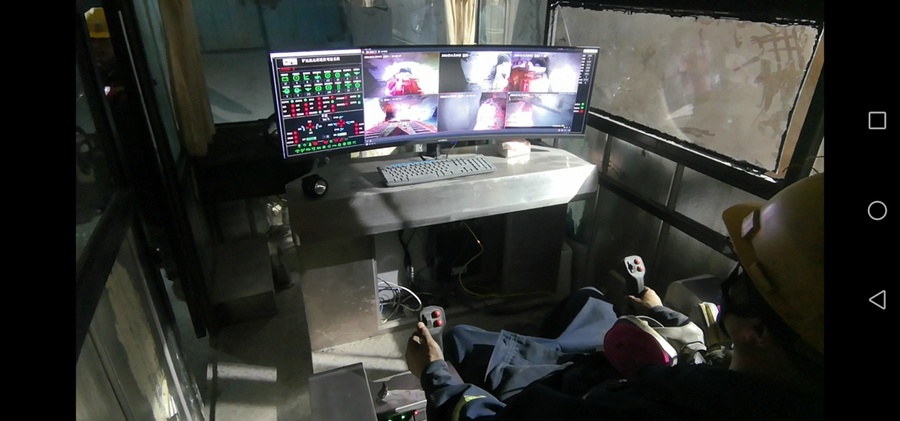