Taking production process as the principal line, based on real-time industrial data such as automation, measurement, and energy; MES runs through professional management process such as production, quality, scheduling, equipment, technology, procurement, sales, and energy, covers twelve functional modules, that is management, technical management, production shipping, production scheduling, production control, product inventory, material management, equipment management, energy management, quality management, measurement management, system management.
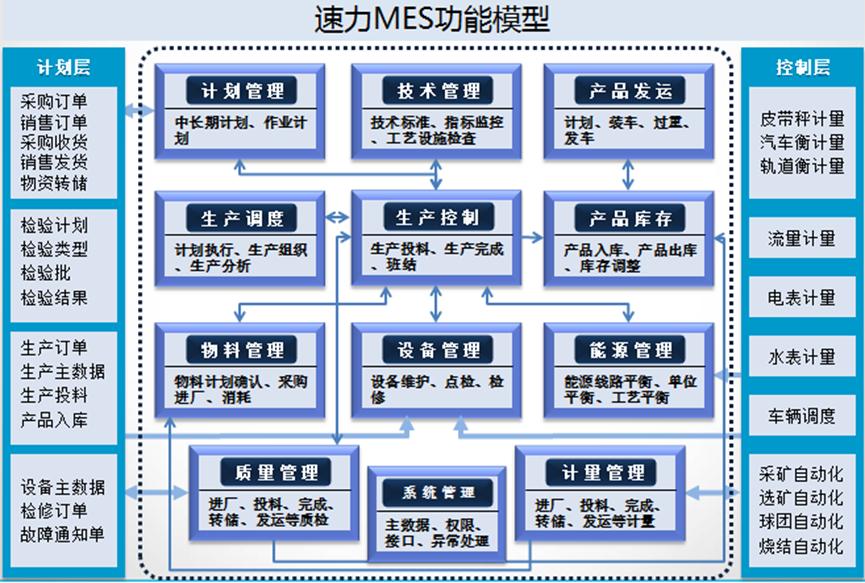
With the rapid development of science and technology, the industry in the world has entered a new development epoch. Germany proposed "Industry 4.0", the United States proposed the "National Strategic Plan for Advanced Manufacturing", Japan proposed the "Science and Technology Industry Alliance", and the United Kingdom proposed "Industry 2050 Strategy", China also proposed "Made in China 2025". The fourth industrial revolution also provides an opportunity to the promoting MES, and the extensive application of ERP and PCS in manufacturing enterprises also provides a good foundation for MES. But for now, the understanding and implementation of MES varies from industry to industry, and the development is unbalanced in different regions. Therefore, industries and enterprises should choose MES suitable for their own development according to their own conditions and characteristics to solve the problems that the traditional manufacturing information systems and process control systems are lack of information connection. Therefore, implementing MES in manufacturing enterprises is of great significance.
First of all, MES is not only an important part of the implementation of Industry 4.0, but also an effective means of deep integration of the two industries which has attracted more and more attention. MES has become the core management system for enterprise transformation, upgrading and sustainable development. Second, the current market situation in the mining industry requires in-depth implementing enterprise fine management, which requires implementing MES that can realize production management informatization in factory, mine, workshop, and manufacturing execution process monitoring informatization. Third, monitoring the mine production process is inconvenient, and the standard of process control stability is difficult to meet. MES realizes the transparency and scientific management of the production process in factories, mines and workshops. It can timely find out the root that causes problems affecting product quality and consumption costs, improve the real-time and flexibility of planning, and at the same time improve the output efficiency of the production line which makes the process line produce the designed output or beyond the design capability.The main management effects are as follows: The management level has been significant improved. Strengthen centralized management, form a collaborative mechanism, and promote collaborative management Weaken functional management and strengthen process management. Promote standardized management and improve execution. Promote refined management and strengthen management intensity. Improve management transparency and increase management binding. The management efficiency has been significant improved The system can reflect production, measurement, quality, logistics and other data timely and dynamically, and can be queried and applied at any time. Data and information are got from the lowest level of measurement, quality inspection, equipment acquisition or automatically generated by the system, which is timely and accurate. Leaders and managers at all levels are freed from a large number of repetitive tasks with low management content. In the past, work that required manual methods and took a lot of manpower and time is now transformed into simple and short-lived work with the help of information technology, and the work efficiency has been improved hundreds of times . Management foundation has been strengthened Provide true and accurate data. From manual input to direct collecting from automated instruments and meters into the secondary database for processing and sorting, the data is transparent whose authenticity can be guaranteed. Accelerate data analysis and response. The system automatically forms a visual report board, which can make you pays attention to the real-time production situation on site in real time at any places.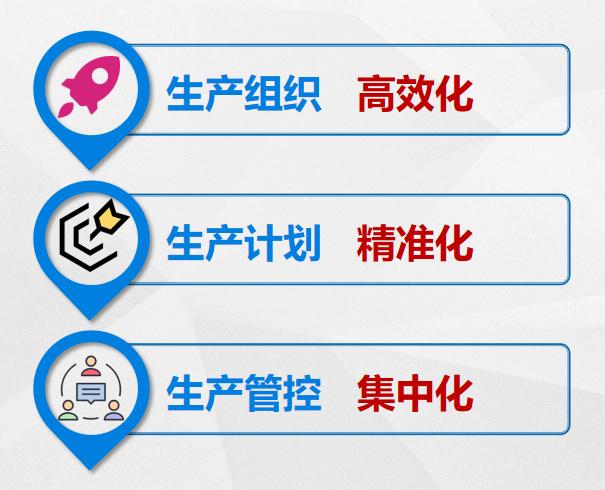
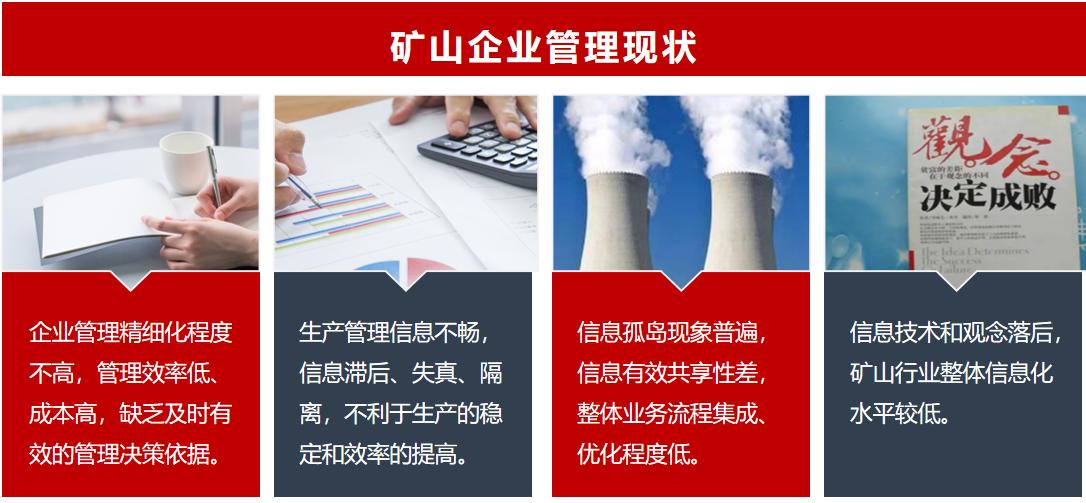